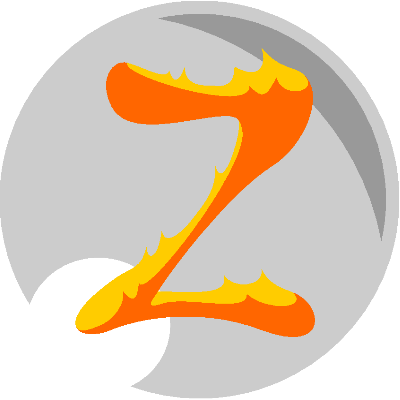
ZET - TechNology
Support in Steel Industry
Blast furnace
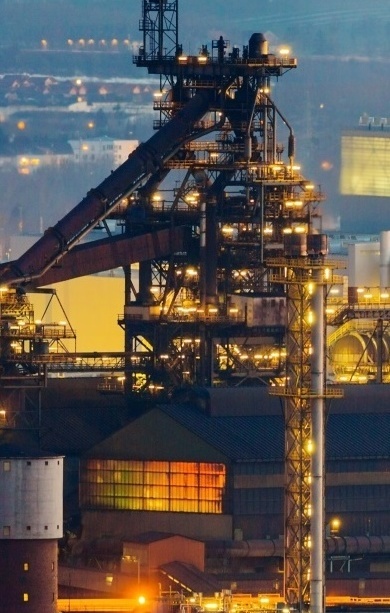
The blast furnace and other reduction processes are still key components for steelmaking and often decide on profitability and success of the entire production.
This also explains the priority to optimize the blast furnace process to its performance limits or to promote the development of alternative production routes.
Process:
- Blast furnace process, metallurgy
- Measures for blast furnace performance and adjustment of the optimal coke rate.
- Installation of temperature monitoring systems for observation and control of the refractory wear profile in the carbon brick area and above.
- Hot blast: Development of blowing technologies for tar, coal, heavy oil, plastic etc.
Equipment:
- Pig iron and slag runner systems
- Dedusting systems on the tapping platform
- Blast furnace diameter enlargements for increased productivity
- Development of tuyeres for injection of carbon carriers such as tar, plastic, heavy oil, coal dust etc.
- Pig iron casting machines (alternative blast furnace route for the cold use of pig iron briquettes)
Refractory:
- Engineering and execution of complete linings of blast furnaces - (frame, C-range, ceramic cup, hot blast, staves, cowper, hot blast line, flue ducts, gutter design)
- Inspection and assessment of the lining condition of the blast furnace
- Blast furnace shaft and rack repairs (stones, concretes or shot-gunning)
- Pig iron runner linings and repairing with SiC concretes
- Cowper repairs during ongoing blast furnace operation
- Design and lining of tuyeres for injection of additional fuels
- Repair and maintenance of all refractory equipment used in blast furnace
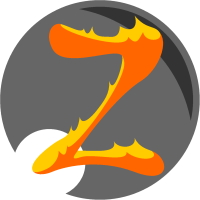
ZET-technology
Support in Steel Industry
8700 Leoben
Austria
email: office@zet-technology.com
www.zet-technology.com