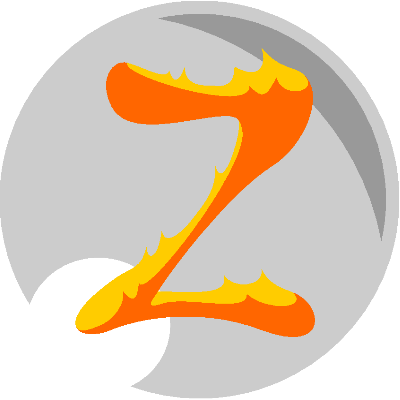
ZET - TechNology
Support in Steel Industry
Continuous casting / CCM
Our experiences range from new construction, revamping, commissioning as well as the operation and optimization of continuous casting plants.

We are competent partner for the optimization of your plant for:
- Billet
- Bloom
- Slab
- Beam Blank
- Horizontal and vertical systems
- Pilot plants
Special "know-how" we have in the area of the mold level control systems, as well as the steel flow from the ladle through the tundish to the mold and the mechanisms that occur.
This know-how was developed by several customers together with the respective technicians, universities and international research institutions and is patented.
The observance of an exact mold level mirror is only one of many requirements in the continuous casting operation to cast high quality steel.
- Avoid "bulging and waving" effects in the mold
- Optimization when casting peritectic steels
- Reduction of micro and macro inclusions in the steel
- Use of various submerged entry nozzles (SEN) and stopper rods ore slide gates and their handling
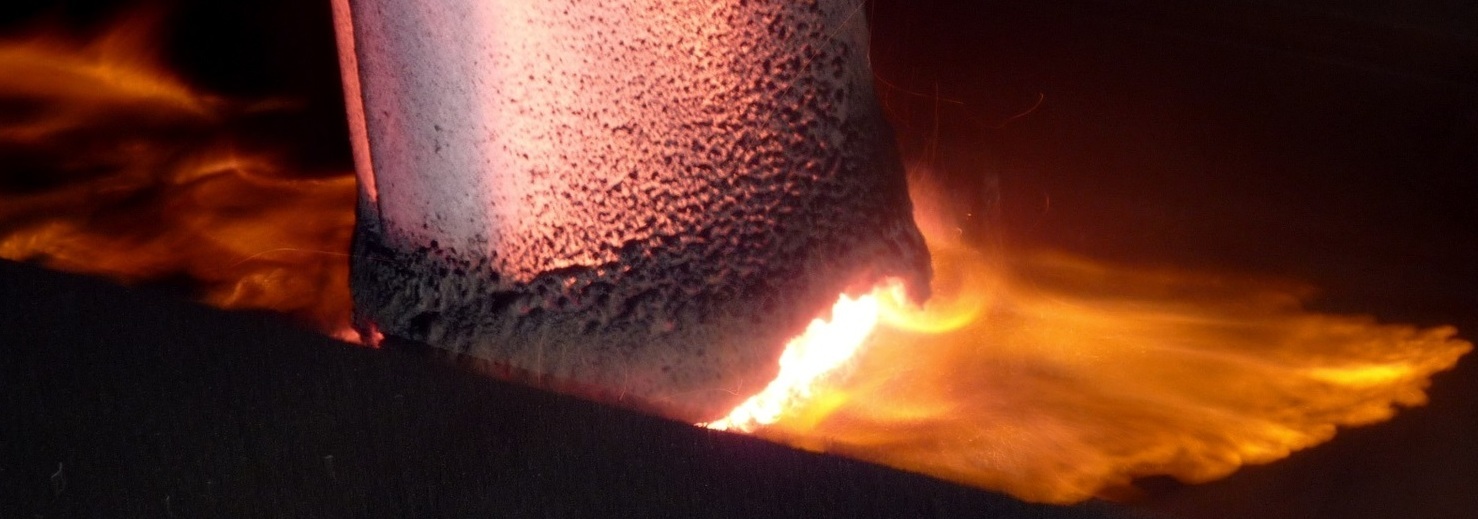
Process:
- Continuous casting process, metallurgy, solidification behavior
- Tundish (geometry, internals, flow simulations, liquid metal models, water models)
- Flow control parameters for highest accuracy (deviation less than 1 mm on the mold level)
- Analysis and optimization of the mold level by considering the entire system of nozzle, stopper rod, mechanism, actuator, mold level signal, different control behavior in Bulging, Waving, Clogging, etc.
- Slide gate, emergency slide gate and immersion tube changer
- Stopper and slide gate control actuator (hydraulic and electromechanical)
- Stopper controls (manual, hydraulic, electric)
- Mold level sensors (radiometric and electromechanical)
- Molds (primary and secondary cooling), breakthrough monitoring systems
- "Soft Reduction" application
- Mold oscillation with different parameters
- Automation of continuous casting plants
Metallurgy:
- Cast critical grades - peritectic steels, mold level control parameters, bulging suppression, casting powder optimization - PATENTED system
- Submerged entry nozzle and shroud (SEN, SES):
- Investigation of flow behavior of the SEN tubes, "clogging" influences and avoidance
- Increase of the SEN service lives
- Flow calculations and simulations (computers and pilot plants)
- Optimization of tundish steel flow, stirring technology in the tundish
- Stirring technology for stopper rod and nozzle plug as well as SEN tube for quality improvement and avoidance of impurities from the atmosphere.
- "Metallurgy" of the tundish
- Electromagnetic stirring in the SEN tube and tundish
- Mold design, taper, materials, modular design
Systems engineering:
- Design primary and secondary cooling
- Strand segments, strand curves, mechanical equipment
- Cooling bed technology
- Casting area, tundish and tundish repair areas
- Tundish preheater
- Design of the tundish steel construction
- Refractory:
- Usage and optimization of all refractory materials at the continuous casting plant
- Tundish (lining concepts, insulating concepts, optimization of the tundish "handling" during drying and heating, during casting and breaking out)
- Shadow tube, shadow tube manipulator
- Stopper and nozzle systems
- Slide gate systems
- Submerged entry nozzle (SEN) optimization, tube changer equipment
Refractory:
- Usage and optimization of all refractory materials at the continuous casting plant
- Tundish (lining concepts, insulating concepts, optimization of the tundish "handling" during drying and heating, during casting and breaking out)
- Shadow tube, shadow tube manipulator
- Stopper and nozzle systems
- Slide gate systems
- Submerged entry nozzle (SEN) optimization, tube changer equipment
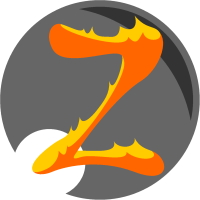
ZET-technology
Support in Steel Industry
8700 Leoben
Austria
email: office@zet-technology.com
www.zet-technology.com